Within the automotive sector, double column machining centres are mainly used for manufacturing dies
|
|
Dear [FIRSTNAME],
Within the automotive sector, double column machining centres are mainly used for manufacturing dies for the production of car body shells. This process poses various challenges as the large workpieces require high dimensional accuracy. More... |
|
TOP STORY |
 |
|
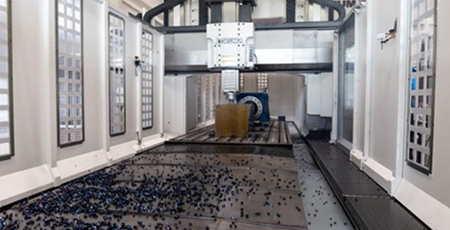 |
Double column machining for the automotive sector
Okuma meets the special demands of the automotive industry. Its double column machining centres provide high precision during the manufacturing of large parts. With over 50 years of experience and a production capacity of 40 units per month, the company is world-leading in manufacturing double column machining centres. Currently, there are over 8,000 Okuma double column machines in use of which roughly 3,500 are used in the automotive sector. Most cars on today’s streets are therefore at least indirectly and partially manufactured by an Okuma machine. More... |
|
TECHNICAL HIGHLIGHT |
 |
|
KAMIOKA: Optimizing machine tools production
Established in 1965, KAMIOKA initially operated as an OEM company and a repair machine shop, under the name of Yongfa. In the past decade, Yongfa gradually converted itself into a research-oriented company and started producing machine tools in-house using their technological knowledge. An exclusive interview with Wen-Hong Huang, President. More...
|
|
Interplay of quality and economy
Anyone who, like HEGGEMANN AG, Büren, concentrates on the development and production of sophisticated metallic lightweight components and subassemblies, is a predestined partner of the aerospace and automotive industry. Since the company was founded in 1962, it has been supplying these two premium industries. It supports customers in all phases of the product development from conception and development through simulation and engineering to prototype. More...
|
|
|
Chamfering despite interference contours
On components such as shafts or idle gears, it was often not possible to use the ChamferCut method for chamfering until now. “Interfering contours, like shoulders, or shaft-work, pose a risk of collision that had restricted the potential use of the tool”, explains Dr Oliver Winkel, Head of the Technology Application. “By tilting the tool, it is now possible to machine gears that had not been possible before.” More...
|
|
Innovative productivity
Okuma has launched the MB-5000HⅡ a horizontal machining center, which offers innovative productivity for global market applications ranging from mass production of automobile parts and other manufacturing sectors. Along with the long, continuous operation made possible by Okuma's trademark high reliability, mass produced parts and small-/mid-sized parts can be machined at the highest level of productivity. More...
|
|
CBN generating grinding – an economic alternative
The demand for high quality gear teeth in areas such as electric mobility, for example, come with great challenges. CBN processes are extremely robust and quality assured, which makes them particularly interesting for the economic production of high quality gear teeth, such as in the area of electric mobility. Attempts are being made to reduce noise, particularly on the very sophisticated electric gears in the automotive sector, by changing the macro and micro geometry.
More...
|
|
AXILE G6 Series to boost your productivity
With continuous development and improvement, Buffalo Machinery has updated its gantry type 5-axis machining center, G6 series to boost manufacturers’ productivity. Buffalo Machinery further extended the structure of G6 and developed 3 different machine concepts to meet various industrial demands, which are G6 Standard, G6 Compact for floor space-saving, G6 APC for automation and G6 MT for mill-turn function. More...
|
|
|
|
|
|
|
|